March 15: A panoramic view of the 100,000-kilowatt solar thermal project in Phase II of the Qinghai-Henan UHVDC Transmission Project, led by Qinghai Gonghe Company. Since resuming construction at the beginning of the year, the group’s first tower-type solar thermal project has fully implemented the group’s “136 Development Strategy” and Qinghai Company’s “128 Work Plan.” With the determination of “starting as if in a sprint, beginning as if in a decisive battle,” the project has seized the golden construction period, spared no effort to meet milestones, and is striving toward the goal of grid connection within the year.
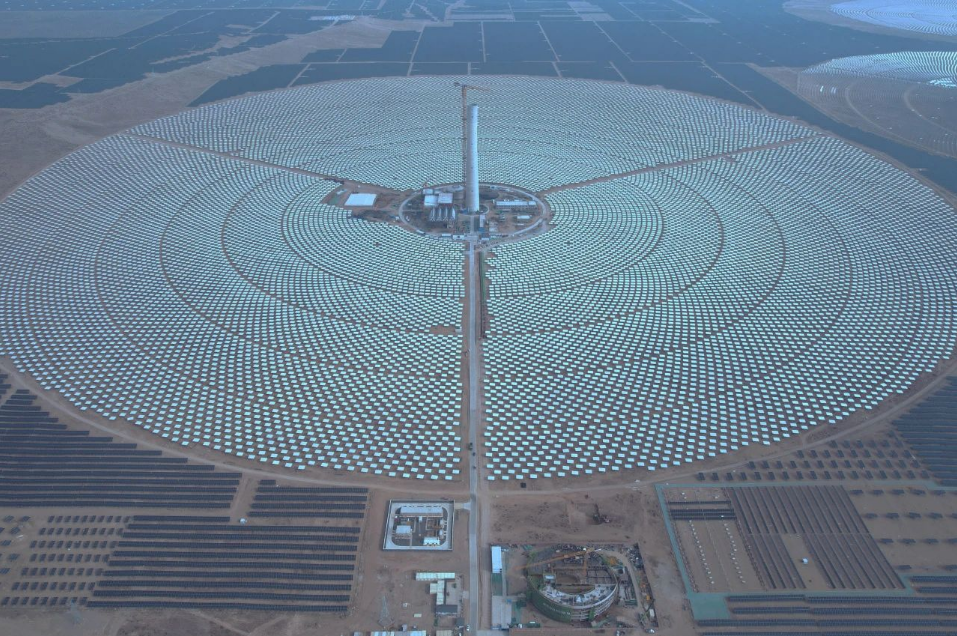
February 16: The generator rotor of Qinghai Gonghe Company’s solar thermal project undergoes insertion into the stator. To win the “first battle” of resuming work and production, the company collaborated with equipment manufacturers to organize installation personnel, repeatedly demonstrating and optimizing the hoisting plan based on on-site operations and safety risks. They carefully inspected lifting facilities and specialized tools, and thoroughly cleaned the stator interior to ensure compliance with installation requirements.

March 15: Over 23,000 heliostats in the mirror field of Qinghai Gonghe Company’s 100,000-kilowatt tower-type solar thermal project in Qinghai-Henan were fully installed. With a total 采光 area (solar collection area) of 700,200 square meters, the company overcame challenges such as high-altitude construction and equipment cold resistance during construction. By optimizing heliostat installation processes and using torque detection and positioning fixtures, they ensured the overall heat collection efficiency of the mirror field through meticulous attention to detail.

March 17: Heliostats of the 100,000-kilowatt solar thermal project in Phase II of the Qinghai-Henan UHVDC Transmission Project. The heliostats are made of ultra-clear float glass and consist of 8 sub-mirrors.
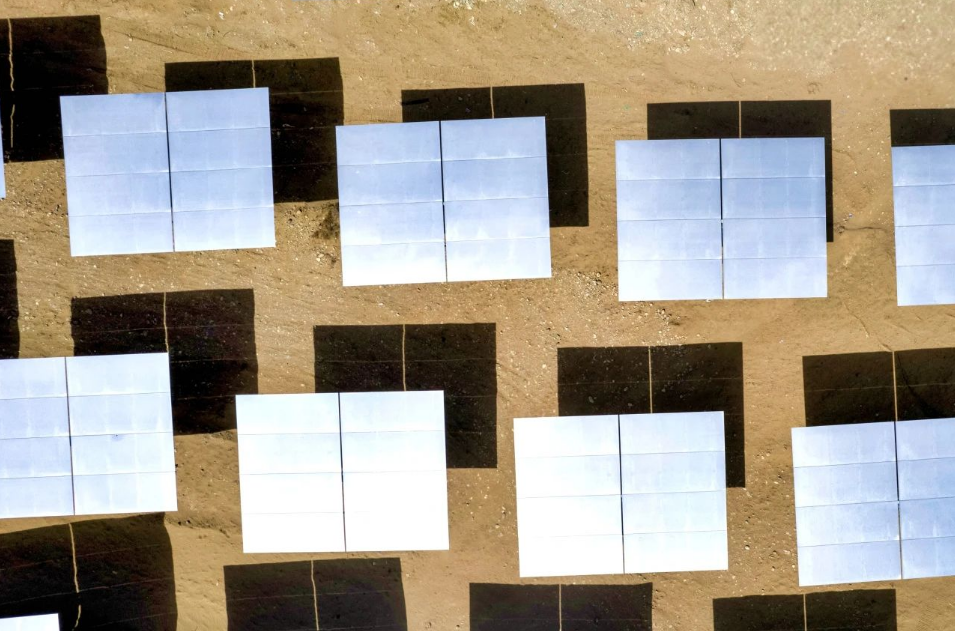
April 7: The lower support structure of heliostats in the project. The project uses high-precision intelligent heliostats that can adjust mirror angles to precisely reflect sunlight to designated positions on the absorber, improving spot quality, reducing energy spillage on the absorber, and significantly enhancing the efficiency of the concentrating solar thermal system to increase power generation.

March 21: Construction personnel at Qinghai Gonghe Company apply anti-seize compound to steam turbine nuts. The project’s steam turbine uses high-efficiency wide-load blade profiles in selection and design, effectively addressing the issue of significant efficiency decline under low-load and variable operating conditions. Additionally, optimizing the flow field of the last-stage blades reduces losses in low-load regions, improves efficiency, and better adapts to harsh conditions such as frequent start-stop cycles and large-scale load regulation in solar thermal units.

March 21: Construction personnel carry out the steam turbine cover closing process. The project team of the solar thermal project planned in advance and organized meticulously, arranging for manufacturers to review key data such as flow passage clearances and shaft alignment in advance. They invited an experienced professional quality inspection team to comprehensively inspect all turbine components and systems, ensuring the cover closing work was completed with zero errors and defects.

April 7: Engineering and technical personnel of the 100,000-kilowatt solar thermal project in Phase II of the Qinghai-Henan UHVDC Transmission Project discuss safety management and quality assurance at the construction site. The company prioritizes on-site supervision and installation quality of major equipment such as steam turbines and generators to build a high-quality project. Meanwhile, it implements risk source prevention and control at the construction site, formulates corresponding emergency plans and measures, maximizes management efficiency, and establishes a joint safety control system.
